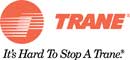
Authorized TRANE Dealer

Leclair Heating & Sheet Metal.
All rights reserved.
2613 McGregor Pl. Thunder Bay, Ontario P7E 5G9
Phone: (807) 623-4655
Oil Furnace types
How a Furnace Works
The basic operating process is the same for all furnaces regardless of the type of fuel they use.
- The thermostat calls for heat and starts the ignition and combustion process. Fuel is delivered to the combustion chamber, mixed with air, and ignited to produce heat in the form of hot gases.
- These hot combustion gases flow through and warm the heat exchanger. The combustion gases exit the furnace and are exhausted from the home.
- A control in the heat exchanger starts the fan which pushes the warm air through the distribution system and thoughout the house.
- This process continues until the room thermostat anticipates enough heat is left in the furnace to bring the house up to the temperature set by the thermostat. The thermostat then tells the burner to shut off. The furnace fan continues to run until the heat exchanger thermostat turns the fan off.
Older "gravity type" furnaces depend upon the natural buoyancy of the hot air to distribute heat within the home. This same natural buoyancy is depended upon to exhaust gases from furnaces. Changes in efficiency of equipment and in the characteristics of homes require that furnaces manufactured today use fans to push the exhaust out of the home.
Gravity Furnace
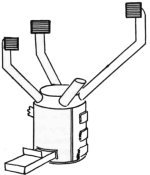
The "Octopus" took up most of the basement, with large pipes running upstairs. Originally coal fired, many were converted to oil and possibly later to natural gas.
The furnace consists of a large cast iron heat exchanger, enclosed in a larger sheet metal cabinet. There is no fan required. The cold air, being heavier than hot air sinks to the floor, through the cold air grates and down to the furnace in the basement, where it is heated and rises through the large warm air pipes to the rooms above.
Being a passive warm air furnace, relying on gravity for air circulation, the temperature in the home is difficult to regulate.
The typical efficiency of this type of furnace is around 1 percent.
Forced Warm Air Furnace
The standard forced air furnace allowed the home owner to reclaim the basement. Not only smaller in size, but installed near the chimney, freeing up all the room previously used by the old Octopus. It was easier to heat the home to a more constant temperature, and it cost less to operate.
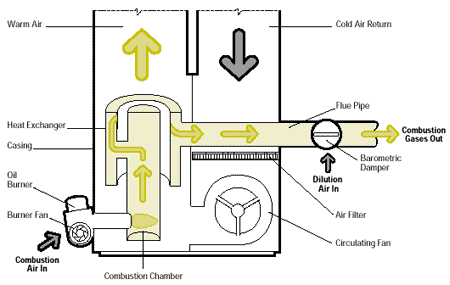
A basic oil-fired, forced-air heating system consists of a burner fed by heating oil, usually from a storage tank inside or outside the house, firing into a combustion chamber in the furnace. The combustion gases pass through the furnace, where they give up heat across a heat exchanger. They are then exhausted to the outside through a flue pipe and chimney.
A barometric damper, acting as a valve in the flue pipe, isolates the burner from changes in pressure at the chimney exit by pulling varying quantities of heated room air into the exhaust. A circulating fan passes cool house air from the cold air return ducts over the furnace heat exchanger, where it is warmed up, then moved into the hot air ducts, which distribute the heated air throughout the house.
Furnaces are rated by their Annual Fuel Utilization Efficiency (AFUE), which is the ratio of the heat output to the total energy consumed by the furnace. The use of a barometric damper to dilute the exhaust gas with house air contributes to the lower AFUE of oil furnaces.
In many houses, the quantity of air drawn through the barometric damper is much greater than required for combustion and can represent as much as 10 to 15 percent of the total heat loss in the house. Thus, anything that reduces this airflow without compromising the performance of the furnace will lead to increased fuel savings and efficiency.
Ever since the fuel price scare of the early 1970s, the industry has been working to improve the efficiency of furnaces and boilers. The introduction of improved burners with flame-retention heads was the first major step in boosting the efficiency of conventional oil-fired heating equipment. Now manufacturers have produced a new "mid-efficiency" class of oil furnace designed to make the most of the superior performance of these new burners.
Mid-Efficiency Oil Fired Furnaces
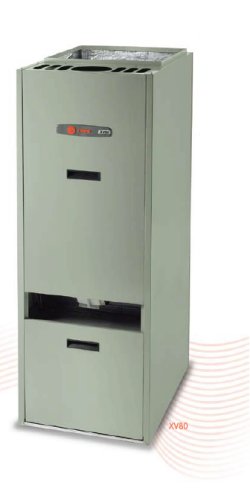
In addition to an improved oil burner, a non-condensing, mid-efficiency furnace features an improved low-mass combustion chamber (usually ceramic fibre) and passes the hot combustion gases through a superior heat exchanger that enables the circulating house air to extract more heat. The need for a barometric damper and the large requirement for exhaust gas dilution by house air have been eliminated in the most efficient designs.
The mid-efficiency furnace must keep the exiting gases above a certain temperature to prevent water vapour in the flue gas from condensing inside the furnace or venting system, where it can cause corrosion and other serious problems. The exit temperature of the combustion gases can be as low as 150°C (302 °F).
Benefits of a good mid-efficiency furnace are much lower combustion and dilution air requirements, as well as more power to exhaust the combustion products (an advantage in newer, tighter housing), a safety shut-off in case of draft problems, and a more effective venting system.
Mid-efficiency furnaces may have a seasonal efficiency of 80 to 85 percent and may use 28 to 33 percent less fuel than an old conventional furnace producing the same amount of heat.
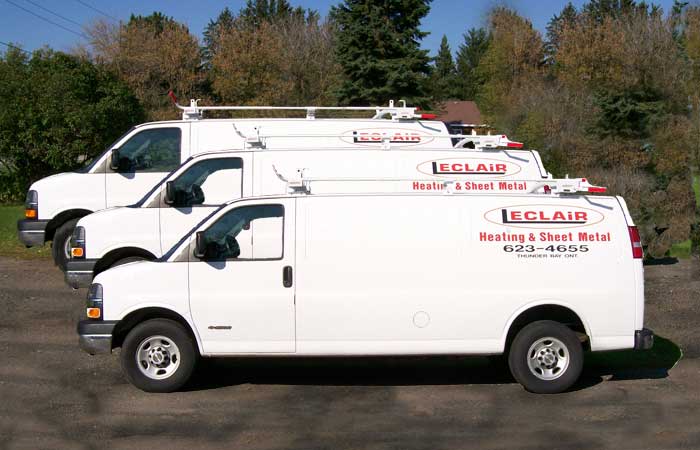